Top 5 biggest Supply Chain pain points - #3 Demand Volatility & Forecast Accuracy
Introduction
In a series of five blog posts, we are going to do a deep dive on the top 5 biggest supply chain pain points, experienced by the business. How did we came up with this top 5? By researching the Internet to look for articles that describe current pain points and keep score of the number of articles. And by the interactions we had with our customers, we listened to the issues they brought to the table.
The top 5 of the biggest supply chain pain points:
-
Lack of end-to-end visibility
-
Rising supply chain costs
-
Demand volatility and forecast accuracy
-
Shortage of raw materials
-
Out-of-stock items
In this blog post we’ll do a deep dive on the pain point ‘demand volatility and forecast accuracy’, what is the impact on the business if not addressed and how it can be solved.
Why is demand volatility and increasing the forecast accuracy so important?
Demand volatility is the variation in demand and most of the time it will hit you suddenly and unexpectedly. Demand volatility makes forecasting future demand difficult and can lead to high stock positions in order to keep up with this unexpected demand. Think about the demand for toilet paper just after COVID started to spread. Shoppers started to buy much more toilet paper compared to the usual buying pattern, resulting in empty shelves and increased production.
Demand volatility can have many causes like recessions, promotions, disasters (see above), but it basically comes down to a changed customer behaviour, their interest in your product. Customers usual bought a predictable amount of products, but suddenly demand declines, maybe due to a competitor with a better product or another product at a lower price.
Forecast accuracy is the measure to calculate how well you predict future demand. Forecast accuracy can be calculated after the initial sale (actuals) by comparing the forecasted demand with the actual demand. The closer the forecast accuracy gets to 100%, the better (100% will be very hard to achieve!).
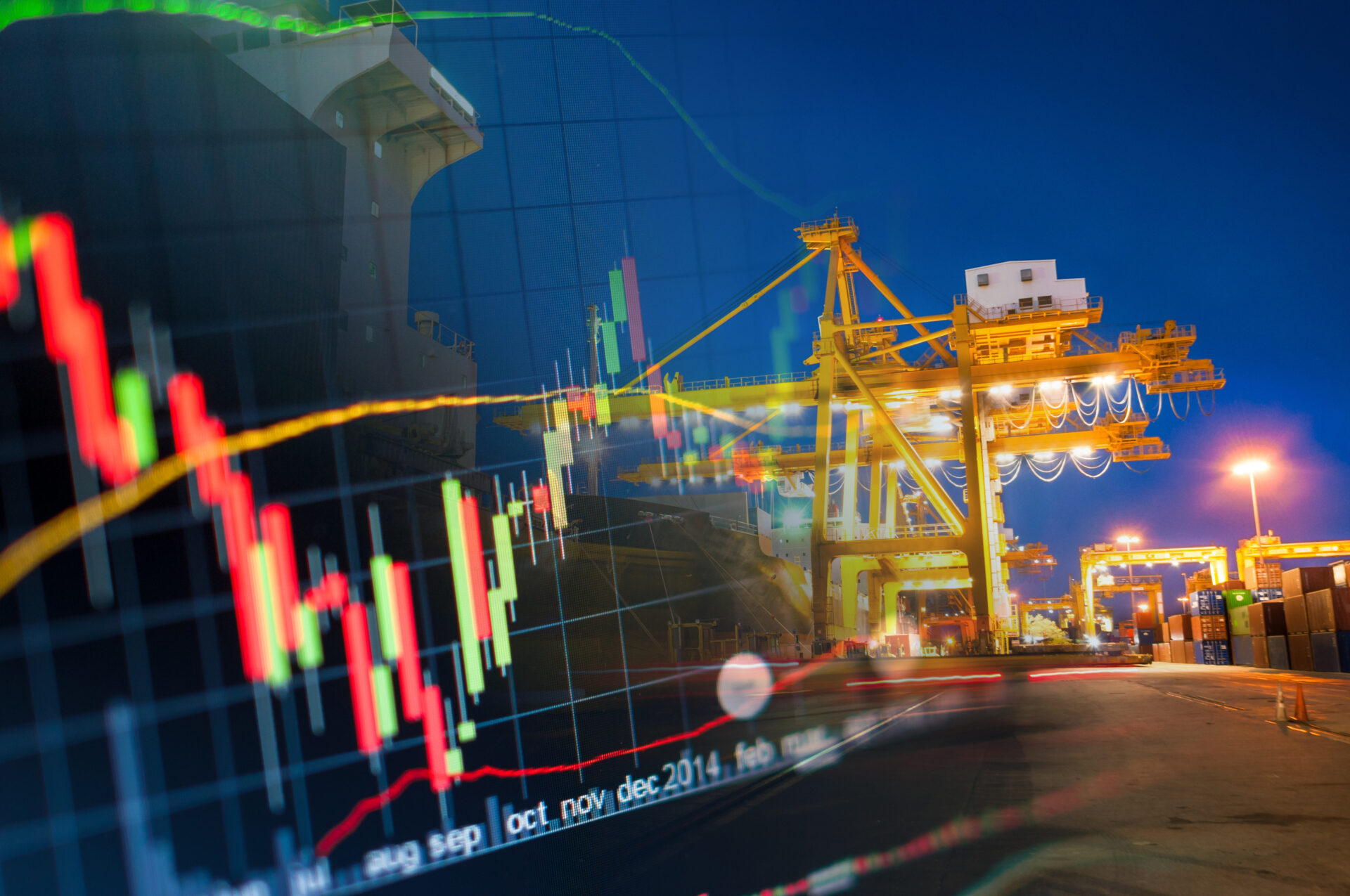
What is the impact of a low forecast accuracy?
Demand volatility and a low forecast accuracy has an enormous impact on supply chain organisations. You could run out of stock by a sudden spike in demand, resulting in lost sales. A typical reaction after a spike in demand is to increase production to keep pace with the new demand. If this new demand is only short lived, you will get stuck with additional stock, with the risk of it becoming obsolete and the high costs of storage (and keeping valuable warehouse space occupied).
If the demand over time varies a lot, it can also mean you have a seasonal pattern. Think of ice creams, which sell much more in summer compared to winter. But seasonal patterns are much easier to predict based on historical data. Any other variation in demand becomes more difficult to forecast. If, for example, a competitor brings a new product to market, demand for your product might fall. You start to innovate and bring a better product to the market. Demand picks up again.
By improving your forecast accuracy, you are able to better forecast future demand and fulfil the demand. A forecast accuracy results (in general) to more optimised stock levels in you warehouse and less lost sales.
How to deal with demand volatility and forecast accuracy
Demand volatility in itself is very difficult to influence. Customers will buy what they need at the time they want it. Promotions, new product introductions can help influence the demand, but when a disaster strikes and customers run for toilet paper, there is little you can do then to accept the new spike and see how you can deliver.
But there are a few ways to be better prepared for this demand volatility and to increase your forecast accuracy:
- AI/ML
- Scenarios
- Reducing lead times
- More agile, resilient
AI/ML
With Artificial Intelligence (AI) and Machine Learning (ML), you can increase the forecast accuracy. Forecasts done by employees are always biased, forecast done by algorithms not. If you can combine actual demand figures with external data (like weather, economic predictions), AL and ML can better predict the future forecast and increase the forecast accuracy. And AI/ ML do not have emotions, they stick to the facts.
Scenarios
Scenarios is the ability to take a copy of your current plan and start to adjust the planning parameters. Scenarios support WHAT…IF-analysis to plan different versions of the future. The advantage of scenarios is that once one comes to live, you are prepared and can respond quickly. You already have gone through the thinking process.
Reducing lead times
If demand suddenly spikes, you want to be able to react quickly. If you have to order semi finished goods from China and have to wait a few weeks before the container arrives, you are too late. By reducing these kind of lead times, you can react faster. In this example, you can start to think of near shoring, bring the production of the semi finished goods closer to your production/ assembly location. In your supply chain, there are probably several areas where lead times play a role. Investigate where and how you can reduce these lead times
More agile, resilient
If you have for one semi finished product one supplier, you have to wait until this supplier can deliver additional components. To become more resilient, you can start to negotiate with other suppliers for the same component. In that case, you can shift demand quickly from one to the other supplier which can deliver the fastest.
And the above mentioned reduction in lead times is also a nice example to become more agile, more resilient.
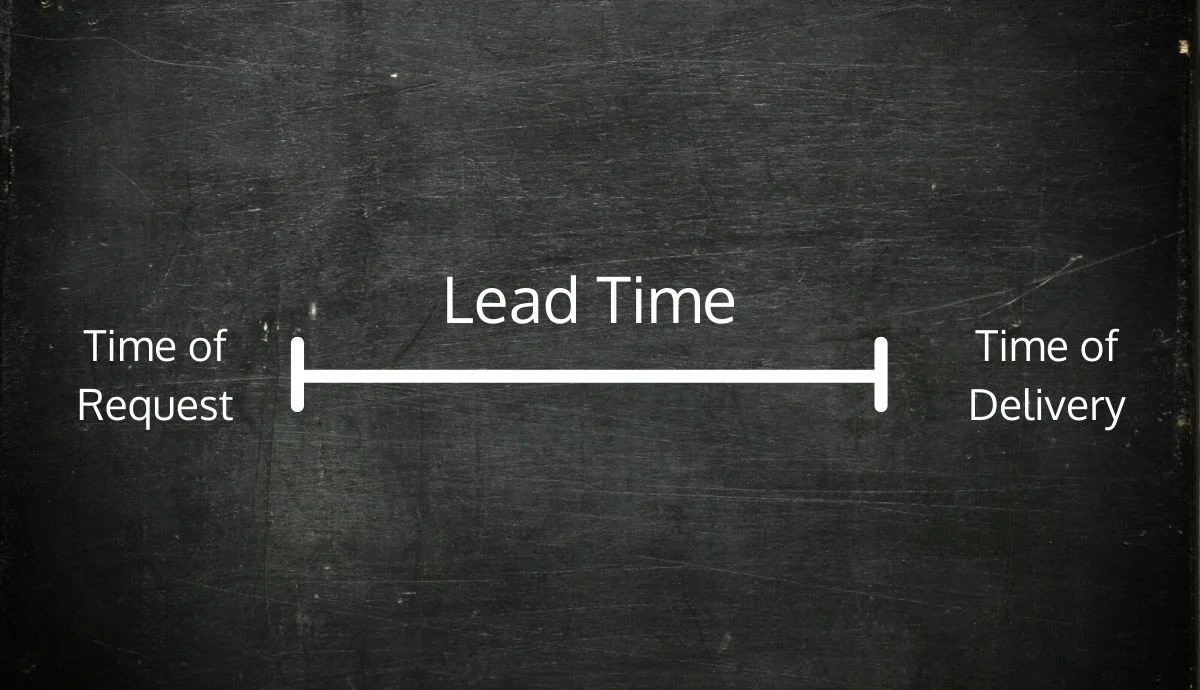
Conclusion
Demand volatility has been increased over the years, making it more difficult for suppliers to forecast the demand and deliver at the right time and place. The better you are prepared by increasing the forecast accuracy and become more resilient, the better you can cope with this volatile demand. And keeping stock levels to an acceptable level.
By analysing your supply chain processes (suppliers, stock levels, forecast accuracy, lead times, etc.), you probably will find areas for improvement to become more resilient, to be better prepared for the volatility in demand. Besides processes, looking at your planning platform can also play an important role. Legacy planning systems and good old Excel are not flexible and in most cases cannot quickly generate a scenario. Latest technology (low-code/ no-code) planning platforms like Pigment can support this needed resilience in planning.
If you want guidance in your search for resilience to cope with demand volatility and increase your forecast accuracy, we are here to help!