Surprising feedback S&OP Flavour Day
S&OP Flavour Day
Each year, Supply Chain Media organises ‘S&OP Flavour Day’, “a crucial event for professionals working in this field, as it provides an opportunity to gain insights from industry experts, discover innovative strategies, and learn about the latest technological advancements that can be applied across industrie” according to their website.
Surprising feedback from thought provoking questions
This year we were present again as one of the sponsors together with Pigment. With a booth in the central location to be able to attract visitors, have conversations and demo the software, it is a very nice event to connect with businesses looking for improvements in their S&OP processes as well as tooling.
Besides the booth and online presence (https://sopflavourday.com), we had the opportunity to do a ten minute presentation main stage. To stick out from the rest of the presentations, we had prepared three thought provoking questions:
- Who is able to run more then three scenarios per planning cycle?
- Who have added their top 20% suppliers to their planning processes & tools to receive early warning signals?
- Who collects the assumptions and decisions made in their S&OP cycle to present these to management and be able to analyse past decision to create a learning organisation?
We expected that out of the 140 attendees, about 20 to 25% would raise their hands per question. We assumed that companies are working on these topics to become more resilient in their planning processes with the support of planning tools. But we were up for a big surprise! To state in supply chain terms: our forecast accuracy was very low!
When we asked the first question, we scanned the room for hands being raised. But after a few seconds it became clear that no one raised their hand. Asking the second question, an estimated 10 to 15% raised their hands as well as for the third question. Our estimate was far off, less then expected attendees could answer yes to one of the three questions.
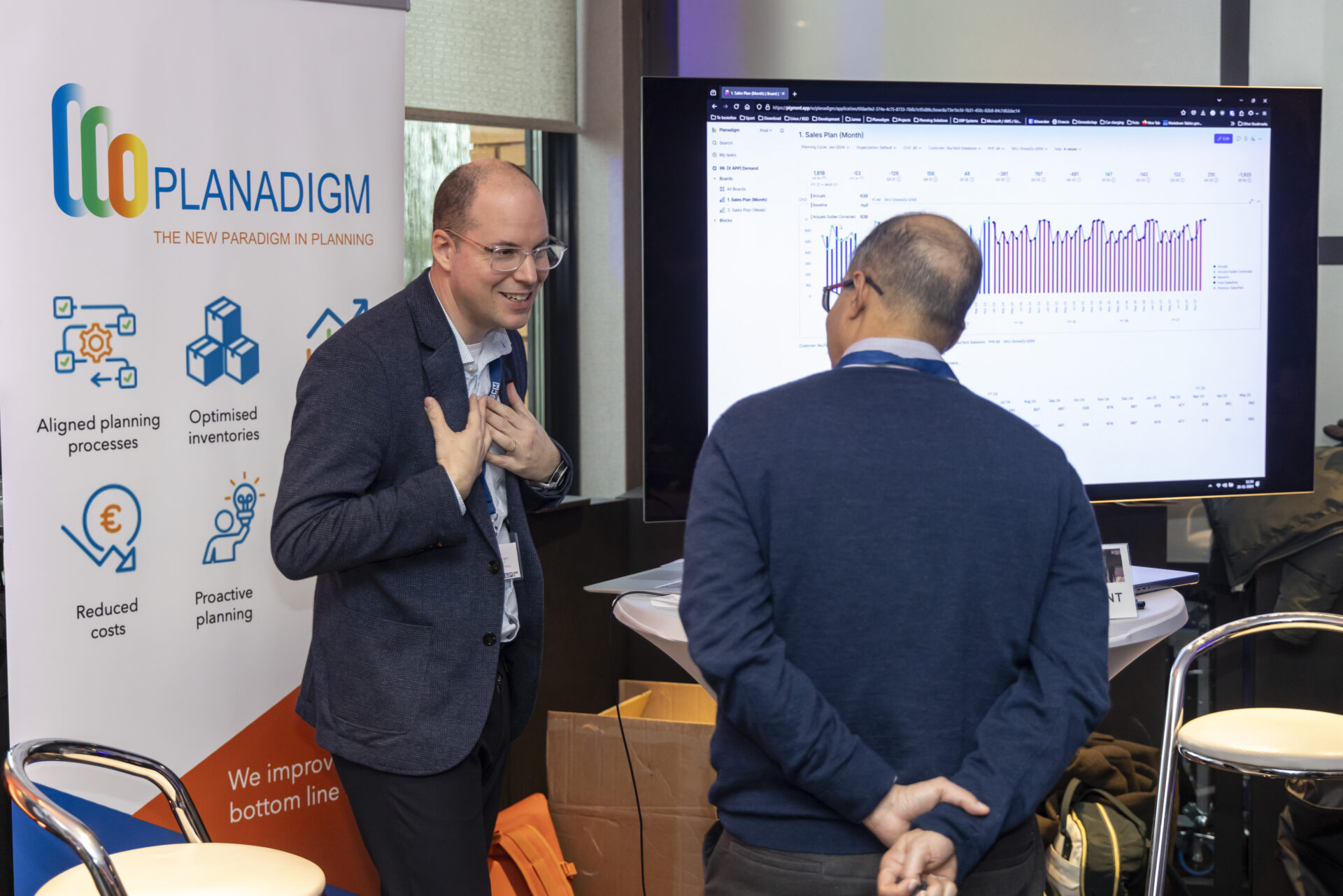
Reasons why companies do not change
Thinking over this feedback to the questions raised made us think: why is there such a huge difference in that we know what to improve in our S&OP processes and tooling and what we actually have implemented? Updating S&OP processes should not be too complicated you might think. Drawing up the ideal process, scrape any non value-add activities, redesign functions and roles and start to implement.
From a tooling perspective, new platforms are out there that allow for scenario creation with just a few clicks, supporting planners with quick insights and analysis. The technology is out there but hardly embraced by organisations. The conditions do ask for a more resilient approach in planning, but companies are not adopting yet. And the need to become more agile, be more resilient in your business planning is greater today then ever before.
So why are we not prepared at the moment to change besides the process and technological capabilities? In our opinion, we believe companies are lacking behind due to:
- Sunk costs
- Old workforce
- Navel gazing
Sunk costs
We probably all know better solutions are out there then the current Excel/ Google Sheets setup or the legacy planning systems that we use today in our organisations. But the investment in time, money and people has been enormous and the willingness to change that and invest in something new is limited. Organisations fear new planning tool implementation based on previous experiences, have an outdated opinion that tool implementation project tend to take very long and are very expensive and that the workforce have to be trained again in the new platform. But with the latest technology out there, all these assumptions, fears and doubts can be counter attacked by choosing the right platform that fits your requirements and budget as well as the right implementation partner. Who understands supply chain and is therefor able to translate that in a flawless implementation.
Old workforce
The supply chain workforce tends to age and retire. The average age of supply chain professionals is rather high, and the older people get, the less willing to change. Being attached to the current way of working is the fear of change, the fear of the unknown that keeps the status quo intact. Also the fear that better processes and/ or tooling might reduce the workload resulting in lay-offs could be one of the reasons why behind the limited willingness to change. By adding young staff to your supply chain team might trigger the required change from within your organisation to look at the current way of working.
Navel gazing
In our opinion the most important factor is that many supply chain professionals are overloaded with operational tasks and issues. Instead of a strategical or tactical focus, day to day operations call for short term solutions, for what we called ‘fire fighting‘ in our recent blog. This navel gazing turns peoples attention completely inwards, 100% operational focused. This does not allow for time to step back, get the much needed helicopter view and reflect. What are we doing here, what causes the disruptions, what can be improved?
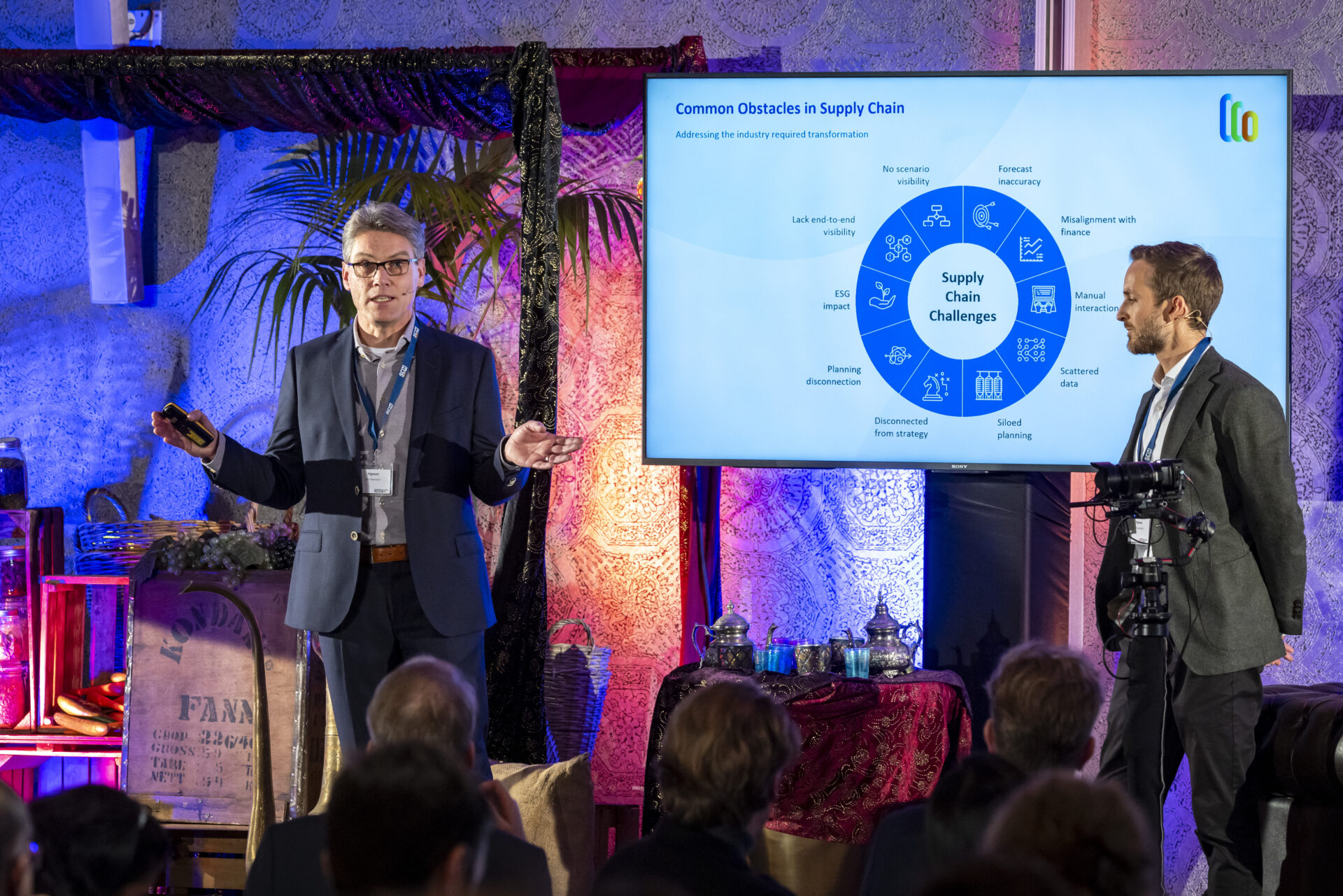
Conclusion
Days like ‘S&OP Flavour Day’ are a great way for supply chain professionals to get out of the operational tasks. Receive insights from other companies, get the latest updates on processes as well as tools, have your ideas and assumptions challenged. And start the thinking process in your organisation and take a step back and answer this question: can we improve our current way of working? If the answer is yes, take the next steps to get things in motion. Doing nothing keeps the current status quo alive and with the many disruptions coming our way, that might not be the right place for you to be in.
The time for change is now and yes, we can support you in your journey to a higher supply chain maturity. Lets connect to see where we can support you to make sure your organisation is resilient and future ready!